Fossil Fuels Beyond Energy: Tracing fossil-based plastics, chemicals, and fertilizers production in China
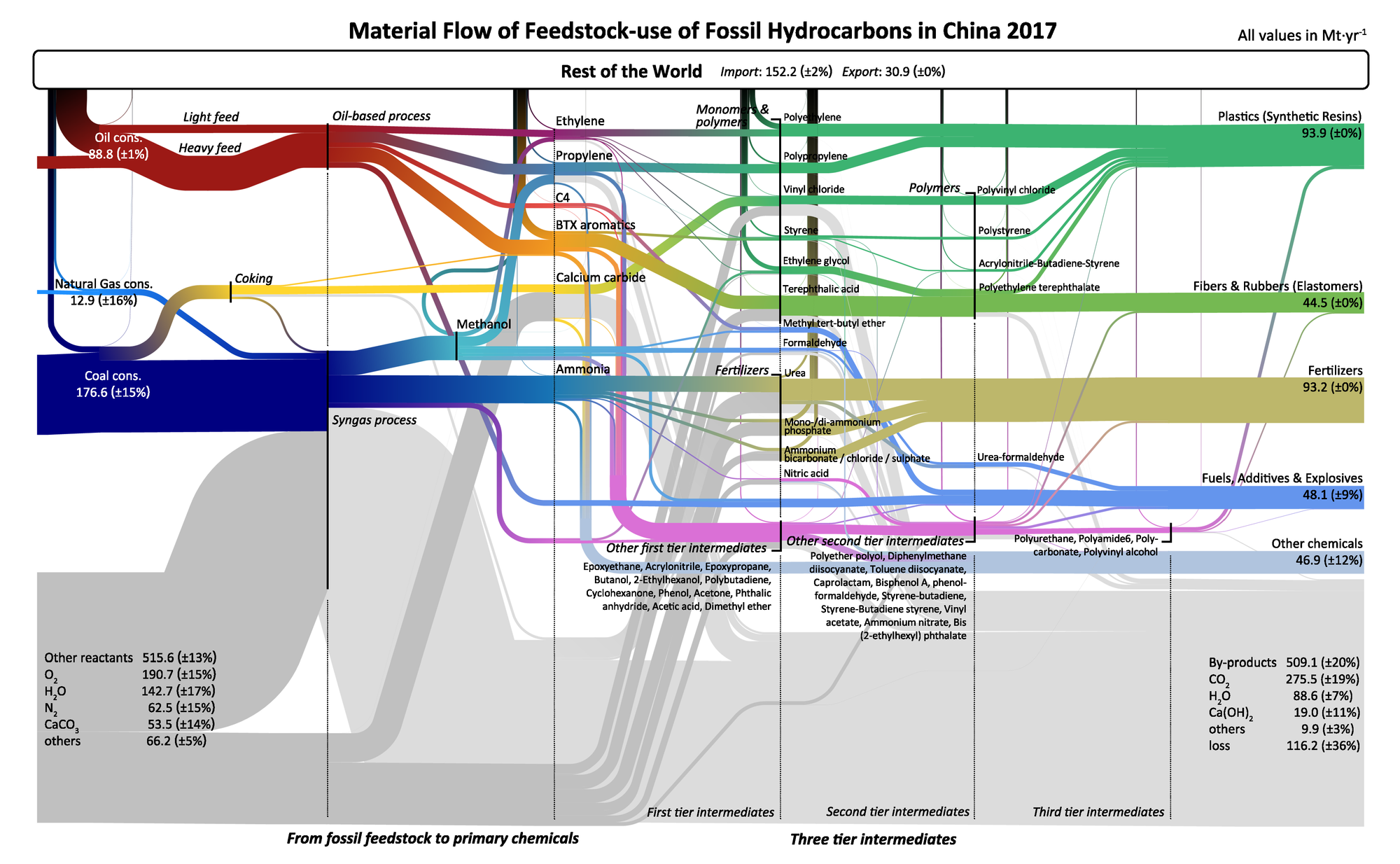
by Meng Jiang and Edgar Hertwich
Fossil Fuels Beyond Energy
Fossil fuels (also referred to as fossil hydrocarbons), encompassing coal, oil, and natural gas, have long been recognized as key drivers of industrialization. Historically, around 90% of global fossil hydrocarbons have been used as fuels for electricity generation, industry, transport, and heating. The remaining 10% serves mainly as raw materials (feedstocks) for the chemical industry, leading to the production of plastics, fertilizers, and a range of chemicals crucial to various industrial processes.
However, as climate action requires a paradigm shift in fossil hydrocarbon usage, countries have reached a consensus to decarbonize their energy sectors by transitioning away from fossil fuels. Many oil giants are pivoting from energy provision to material manufacturing, with most new chemical complexes leveraging oil-to-chemical (OTC) technology that can transform up to 70%-80% of crude oil into high-value chemicals.
Despite these shifts, the metabolic patterns of fossil resources, especially in the complex chemical industry, have not been thoroughly explored. This knowledge gap stems from the inherent diversity and complexity of chemical products and production processes.
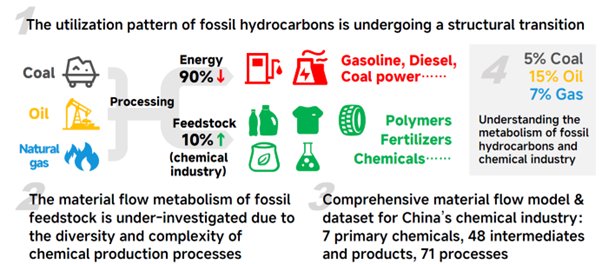
Complexities of China’s Chemical Industry
China plays a critically important role in the global chemical sector due to its world's largest production volume, comprehensive process network, and high fossil hydrocarbon consumption.
Generally, crude oil and natural gas constitute the primary fossil feedstocks in the chemical industry. In China, most downstream chemical products are derived from crude oil through petrochemical processes. Approximately 70% of the oil and 37% of the gas required to meet demand are imported due to limited domestic oil and natural gas resources. Hence, coal is also used as an important feedstock, specifically utilized, for example, for producing methanol and generating hydrogen for ammonia synthesis. As such, most chemical products manufactured in China are still oil-based.
To better understand the complexity of China’s massive chemical production systems, researchers from Tsinghua University, NTNU Indecol, and other collaborators developed a tailored process-based material flow model for China. The model highlights the interconnected mass and carbon flows within the expansive gate-to-gate production network, encompassing seven primary chemicals, 48 intermediates and final products, and 71 major production processes.
This analysis revealed the material flows of coal, oil, and natural gas across the production chain, providing estimates of direct and indirect CO2emissions. In 2017, China’s chemical industry used 90 million tons of crude oil, 13 million tons of natural gas, and 180 million tons of coal, as feedstock, constituting 15%, 7%, and 5% of China’s respective total consumption. Process emissions from primary chemicals in 2017 amounted to 300 million tons of CO2, while energy-related emissions (from primary chemicals) were slightly higher at 340 million tons.
As China seeks to reduce CO2 emissions without increasing oil and gas imports, improving energy efficiency, shifting to renewable and nuclear power, and utilizing green hydrogen will be crucial. The remaining emissions can be tackled with carbon capture, utilization, and storage (CCUS).
Look into the Future and Stakeholders' Engagement
The chemical industry plays a significant role in the structural transition from fossil “energy” to fossil “feedstock”, given the world's climate ambitions. The complex material flow of fossil feedstock to products revealed by this study significantly enhances our understanding of fossil hydrocarbon metabolism. It also provides a solid foundation to connect supply-side and demand-side solutions in future investigations into the industry's decarbonization.
The scale of China's chemical industry is expected to continue expanding in the foreseeable future. Consequently, greater efforts will be required for energy conservation and emission reduction. Converting coal to chemicals requires large-scale hydrogen substitution, which is energy-intensive when using water as the hydrogen source. Part of the carbon in the feed is oxidized to absorb the oxygen from the water molecules. Green hydrogen could drastically reduce emissions—by up to 68% compared to traditional processes.
Given that much of China's chemical production is situated in coal-rich regions with significant renewable energy potential, integrating green technologies makes sense. This approach leverages existing infrastructure and shifts facilities towards more sustainable practices without starting from scratch. However, scaling up these new technologies to meet the 2030 timeline will present significant challenges, requiring a blend of innovation, investment, and commitment.
Continuous collaboration with industry experts is essential to refine strategies that enhance energy efficiency, integrate sustainable practices, and promote a circular economy. Dialogue with practitioners on decarbonizing the chemical sector revealed a difference in outlook compared to environmental experts. This disparity may stem from varying perspectives on the industry, differing interpretations of economic and technological factors, and the overall complexity of sustainability considerations. This contrast underscores the need to challenge current norms and incentivize pragmatic decarbonization. Regular reviews and models that account for regional differences in production methods are crucial as the industry expands. Moreover, shifting consumer behavior to reduce plastic waste and support circular flows will be vital for achieving effective decarbonization.
The research, led by researchers from Tsinghua University and NTNU Indecol, was recently published in Nature Communications.
Article Link: https://www.nature.com/articles/s41467-024-47930-0